El Mantenimiento Industrial por el Ing. Alejandro J. Pistarelli
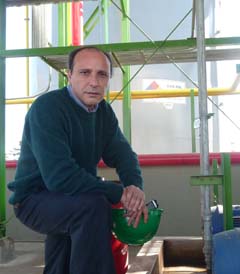
Nuevo Seminario: Excelencia en Mantenimiento para PYMES (GA-12)
Todos nuestros Cursos se ofrecen también Online y en Vivo!
Evolución del Mantenimiento
Desde que el hombre comenzó a fabricar objetos para uso personal, le fue imprescindible llevar a cabo alguna restauración para volver a utilizarlos. Así fue que conforme se evolucionó en tecnología, también se evidenciaron avances en las maneras de restaurar objetos, herramientas y máquinas.
Ya a comienzos del siglo XX la industria se tornó cada vez más mecanizada, y aunque los niveles de producción eran bajos, se realizaban tareas de limpieza y lubricación a cargo del mismo personal que operaba las máquinas. Estas estaban por lo general sobredimensionadas respecto a las necesidades del mercado. Básicamente se aplicaba la corrección frente al defecto o lo que hoy conocemos como Mantenimiento Correctivo.
Sin embargo, fue a partir de 1950 cuando la demanda global de bienes de consumo aumentó de forma abrumadora. Los procesos industriales se hicieron cada vez más intensivos. Las detenciones provocaban grandes pérdidas económicas a las compañías. Aumentó la mecanización, la automatización y la competitividad. Ya no había posibilidad de aprovechar los tiempos muertos de producción; sencillamente porque no existían. Surgió, entonces, la idea de prevenir las fallas. Anticiparse a su ocurrencia, para que no produjeran un perjuicio mayor. Así, se capitalizó la primera gran especialización en mantenimiento. El personal de producción se dedicaría exclusivamente a operar el equipo logrando su máximo rendimiento; mientras que personal especializado en reparaciones, estaría dispuesto tanto a corregir y restaurar las averías una vez sucedidas, como a intentar prevenirlas. El Mantenimiento Preventivo de recambio o restauración fue tomando cada vez más protagonismo, llegando a la década del 60’ a ser el más aplicado y difundido.
A partir del avance de la electrónica y del mejor entendimiento sobre los patrones de falla, surge y se fortalece el Mantenimiento Condicional basado en el monitoreo del estado de funcionamiento del equipo (o alguna de sus variables de proceso) que permite aprovechar al máximo el beneficio de cada activo antes de retirarlo de servicio.
Los requerimientos de disponibilidad y eficiencia que la realidad actual impone, obligan a optimizar y evaluar todas las herramientas capaces de reducir los tiempos muertos por paradas no programadas. Existen, entonces, una batería de estrategias capaces de controlar las consecuencias de los fallos y asegurar el cumplimiento de las normas de seguridad y medio ambiente. Un ejemplo lo constituye el Mantenimiento Detectivo que puede ser una alternativa válida para el control de los fallos, sobre todo para aquellos que involucran un alto riesgo industrial. Dicha estrategia permite descubrir y mitigar las consecuencias de las fallas que ocurren sobre dispositivos Redundantes o de Protección.
El Mantenimiento y la Sociedad
Es de público conocimiento que cada día se hace mayor la necesidad de identificar y controlar potenciales eventos (sucesos) que, aún con baja probabilidad de ocurrencia, tienen consecuencias muy graves. Esto cobra mayor importancia todavía en las organizaciones cuyos procesos son de alto riesgo. Las evaluaciones probabilísticas de riesgo buscan cuantificar las consecuencias de los fallos con gran impacto en la seguridad personal, en el medio ambiente o en los intereses económicos de un sistema; lo cual obliga a efectuar estimaciones que envuelven cierta incertidumbre. Muchas veces, es preciso valerse de datos estadísticos de componentes similares que actúan en contextos operativos diferentes, perdiendo así las posibles interferencias (acoplamientos) sistémicas cuyas consecuencias pueden ser aún peores que la de los propios modos de falla actuando por separado.
Las organizaciones modernas, y la sociedad toda, están tomando cada vez más conciencia del Riesgo y hay cada vez más interés en controlarlo. Controlar el riesgo no significa eliminarlo por completo. Se trata de un parámetro probabilístico, cuya valoración es subjetiva. No se lo puede medir pero sí estimar en muchos casos. El riesgo que una persona está dispuesta a tolerar (potencial peligro), es función del grado de control personal que se tenga sobre el proceso. A medida que el control sobre el proceso riesgoso disminuye, también disminuye la tolerancia que se tiene. El riesgo individual es diferente al riesgo social. Las personas, por lo general, tienen menos tolerancia al riesgo social que al individual. Por ejemplo, y aunque la tasa de accidentes indique lo contrario, un conductor está dispuesto a tolerar mayor riesgo si es él quien conduce (se suele no ser tan exigente con uno mismo); lo contrario sucede si viaja en un transporte público de pasajeros (se suele ser muy exigente con la empresa y el conductor). La tolerancia al riesgo es menor por ser mayor la exigencia. De cualquier manera, cuando un riesgo no es controlado, pueden ocurrir serios daños.
El tipo de riesgo que se da en el ámbito industrial (y con el que, además, debe convivir el Mantenimiento Industrial) se denomina riesgo desfavorable dado que siempre se está en una situación potencial de pérdida. Las organizaciones se encuentran de cara a perder o no perder, pero nunca de obtener un beneficio adicional (ganar). El riesgo favorable sólo se presenta en los juegos de azar.
El riesgo es la probabilidad de que un suceso no deseado (potencial pérdida) provoque un accidente durante la realización de una actividad determinada, y cuyas consecuencias son cuantificables.
Confiabilidad
Uno de los dos atributos para garantizar la disponibilidad, es [...]